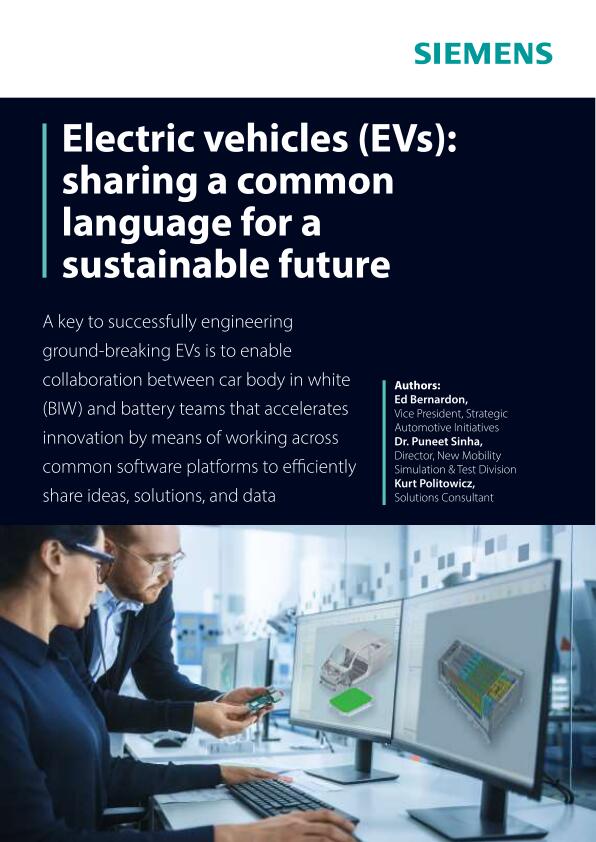
Electrical automobiles (EVs): sharing a typical language for a sustainable future
The local weather disaster is turning into more and more urgent, and demand for electrical automobiles (EVs) is booming. Engineering these EVs calls for brand new methods of working: as we transfer in the direction of the electrical future, battery and physique in white (BIW) groups might want to work collectively for the primary time.
This whitepaper critiques the distinctive challenges that include the EV engineering course of all through its main phases, introducing the engineering necessities of integrating a battery pack into automobile design. It then presents the answer: to implement a typical engineering software program platform to permit totally different groups to work seamlessly collectively. Producers which embrace this chance will thrive within the electrical future.
by Siemens VMS
Thanks.Please examine your e mail to obtain the Whitepaper.
This stage contains the next steps:
• Pack thermal administration optimization.
• Battery pack thermal runaway evaluation to make sure a sleek failure.
• Validation of battery power and thermal efficiency in opposition to automobile necessities.
• Battery administration system (BMS) embedded software program growth and validation.
Thermal administration optimization is performed to make sure cell-to-cell temperature variation, to take care of most temperature inside specification, and to confirm that the battery pack meets all thermal and power necessities. Engineers use computational fluid dynamics (CFD) simulation options to optimize thermal administration methods, guaranteeing it meets necessities for vital operation situations.
The design should guarantee what known as a “sleek failure” to keep away from hearth within the occasion of a number of cells failing. Security concerns embrace methods to restrict temperature spikes in a major variety of cells if one cell within the bundle undergoes a thermal runaway occasion. One other hazard that have to be thought of is the unfold of battery pack gases that will vent into the cabin. Slowing the unfold will enable time for passengers to exit the automobile.
Battery pack security testing is vital; nevertheless, it doesn’t clarify why a design might fail. Pack security simulations provide perception on the place limitations is likely to be discovered and methods to tackle any operational points, thereby strengthening the design course of.
Massive battery pack security testing is difficult. Security simulations that account for chemical reactions, transient temperature unfold, and the small print of pack structure geometry are very important to make sure a secure operation. Additionally it is vital to evaluate the influence of any pack geometric adjustments to fulfill thermal efficiency on automobile integration and packaging.
Battery pack validation
As soon as the thermal administration of the battery pack has been optimized the EV teamwork with the techniques engineers to validate {the electrical} and thermal efficiency of the battery pack throughout the full automobile system. Solely then is the battery pack design fastened.
For this collaboration, a digital continuity and built-in workflow between detailed three-dimensional (3D) battery pack design evaluation and one dimensional (1D) automobile system evaluation is used. Central to the success at this stage is bringing battery-specific evaluation to system simulation with out slowing down computation. Extracting lowered order fashions (ROM) and integrating it right into a system simulation achieves a large enhance in velocity.
This built-in 1D-3D workflow permits engineers to validate drive vary for a whole drive cycle with life like energy demand, together with calls for from cabin cooling and different auxiliary energy. Engineers also can reliably estimate change in vary at totally different ambient temperatures.
Creating the mind
The battery administration system (BMS) is the mind of a battery pack and might be developed similtaneously the pack’s mechanical and electrical techniques are being designed. there are 4 key parts for BMS algorithm and software program engineering:
1. Software program requirement administration and course of orchestration for growth and validation.
2. Correct algorithms to estimate state of cost, state of well being, remaining drive vary, in addition to algorithms for cell balancing and thermal administration are developed. These algorithms must account for cell chemistry and efficiency.
3. Algorithms then have to be reworked into embedded software program. Poorly architected software program introduces errors that trigger recall and legal responsibility dangers. As soon as the software program structure is designed, embedded software program integration wants to make sure AUTOSAR implementations, producing actual time executables (RTEs) and cyber safety.
4. In depth testing of BMS is vital. Engineers more and more depend on Software program-in-the-loop (SiL) and {Hardware}-in-the-loop (HiL) testing to validate BMS software program earlier than launch.
The power to replace BMS simulation with a brand new mannequin reflecting any battery pack structure design adjustments advantages design effectivity. The objective of this stage of the method is a verified, signed-off battery pack design.
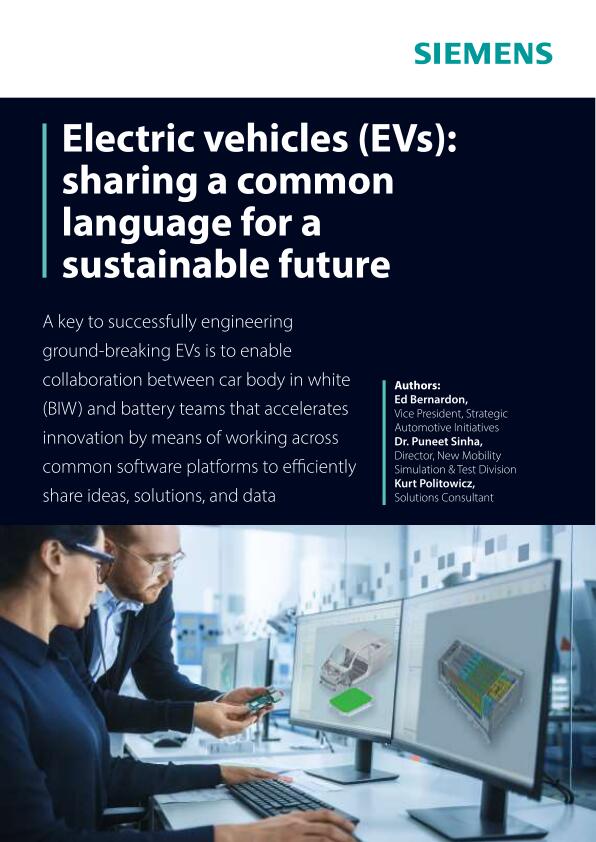
Electrical automobiles (EVs): sharing a typical language for a sustainable future
The local weather disaster is turning into more and more urgent, and demand for electrical automobiles (EVs) is booming. Engineering these EVs calls for brand new methods of working: as we transfer in the direction of the electrical future, battery and physique in white (BIW) groups might want to work collectively for the primary time.
This whitepaper critiques the distinctive challenges that include the EV engineering course of all through its main phases, introducing the engineering necessities of integrating a battery pack into automobile design. It then presents the answer: to implement a typical engineering software program platform to permit totally different groups to work seamlessly collectively. Producers which embrace this chance will thrive within the electrical future.
by Siemens VMS
Thanks.Please examine your e mail to obtain the Whitepaper.