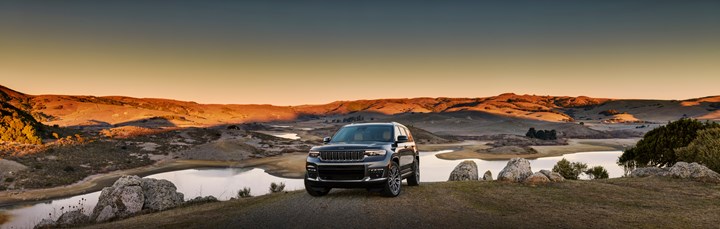
As automakers search to cut back the curb weight of typical and electrical autos (EVs), steel chassis elements have turn into a big goal for conversion to composites or hybrid techniques. Picture Credit score: Stellantis
All the simple automotive functions had been transformed from glass and steel to plastics and composites way back. What are left are primarily structural functions on the chassis with significantly greater efficiency necessities than inside trim and exterior physique panels and numerous trim elements.
Then again, stored in incumbent metallic supplies, chassis elements contribute considerably to traditional and electrical automobile (EV) mass and carbon footprint, and in consequence, have turn into key targets for the conversion to composites and hybrid techniques that mix a number of supplies — typically steel and composites or a number of forms of composites — because the 5 functions that observe will exhibit.
In every case, the shift from metals to composites or hybrid composite elements met or exceeded benchmark mechanical efficiency whereas lowering mass and tooling prices, eliminating corrosion issues and very often enhancing noise/vibration/harshness (NVH). And all of those functions are used on high-volume automobile platforms the place affordability is a big contributor to success.
Off-road stability
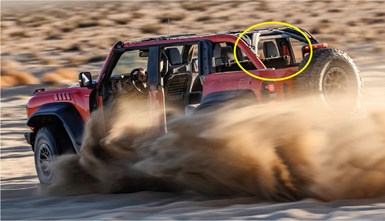
To deal with the wants of off-road prospects, particularly these driving within the desert, Ford and its suppliers developed a composite C-brace to attach left and proper D-pillars to the rear roof cross-member. The Class A visual half will increase rear torsional rigidity and automobile dealing with whereas lowering mass considerably versus benchmark aluminum and metal. Picture Credit score: Ford Motor Co.
An fascinating and visual composite utility for off-road lovers may be discovered on the 2022 Ford Bronco Raptor sport utility automobile (SUV) from Ford Motor Co. (Dearborn, Mich., U.S.). The element, known as a C-brace, is a completely purposeful structural brace that joins left and proper D-pillars within the rear cargo space with the rear roof cross-member to extend stiffness and torsional rigidity all through the automobile. Whereas “off-roading,” the brace additionally helps cut back vibration switch, which, in flip, can enhance dealing with and decrease NVH.
To deal with the wants of off-road prospects, significantly these driving within the desert, Ford engineering set a objective of accelerating automobile torsional stiffness by 40% to enhance automobile dealing with and NVH traits. When prospects had high and facet/door panels off, the brace can be extremely seen within the open cockpit, so sustaining Class A aesthetics — particularly beneath long-term warmth and UV publicity — had been essential.
Further specs had been that the brace wanted to fulfill all rear visibility necessities and never block the driving force’s view, it needed to enable the entrance passenger doorways to be stowed securely and compactly within the cargo space with out injury and it needed to obtain a spring fixed/rotational stiffness worth of 550 kilonewton-meters per radian within the lightest potential bundle, particularly given the weight-sensitive roof location that might shift the automobile’s middle of gravity up or down.
A crew comprised of Ford, Tier 1 integrator/molder Montaplast of North America Inc. (Frankfort, Ky., U.S.), supplies suppliers BASF Corp. (Florham Park, N.J., U.S.) and 3M Co. (Maplewood, Minn., U.S.) and toolmaker Industrial Instrument Group (Comstock Park, Mich., U.S.) collaborated to design the Class A all-composite brace.
In depth non-linear structural evaluation was performed all through the event section to optimize styling and look and to confirm structural efficiency would meet desert sturdiness, load displacement and stress necessities at various temperature, roof load and torsional stiffness values, in addition to to develop bonding choices.
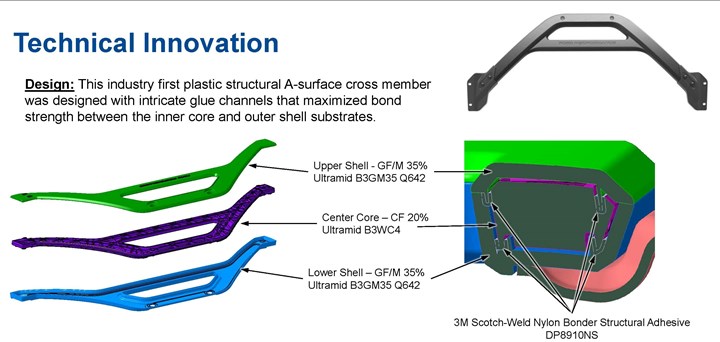
Intricate tongue-and-groove-like glue channels had been molded into each the shells and the core to maximise bond power between core and skins. Montaplast additionally designed and constructed a robotic, temperature-controlled adhesive dishing out system to fulfill meeting necessities, together with precision glue path, bead profile, circulation fee and blend ratio. To satisfy Ford’s harmonized shade necessities for a Class A exterior floor, the outer shells are painted black. Picture Credit score: Ford Motor Co.
Initially, a two-piece design was developed, which developed right into a three-piece design that was additional refined into what the crew known as an superior three-piece design. The latter is a sandwich with a core injection molded from 20% quick carbon fiber-reinforced polyamide 6 (CF/PA6) — Ultramid B3WC4 — and skins/outer shells injection molded from 35% quick fiberglass-reinforced PA6 (GR/PA6) — Ultramid B3GM35 Q642. The polymer system was particularly chosen to fulfill Ford’s off-road desert sturdiness necessities. A newly formulated methacrylate adhesive (3M DB8910NS) that’s stated to be quick curing, versatile and warmth steady is used to bond all three elements collectively.
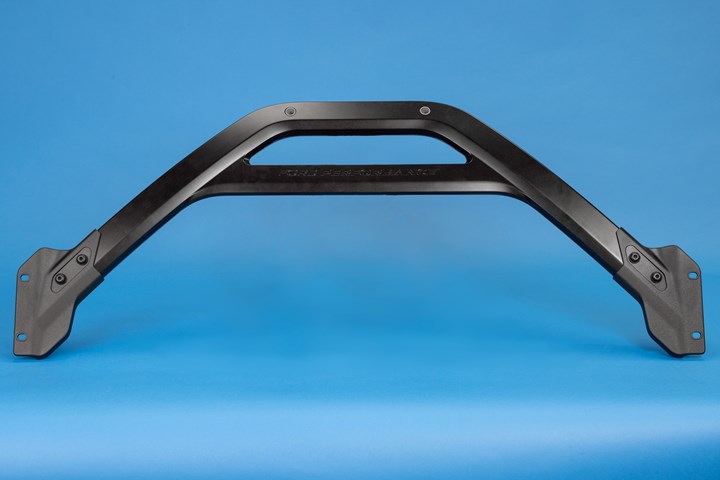
The ultimate brace options a number of design-for-assembly options, together with self-centering polyvinyl chloride (PVC) foam, sliding L-brackets in stamped metal and slotted die-cast aluminum brackets to accommodate physique tolerance variations and guarantee match to the physique rails. Picture Credit score: SPE Automotive Div.
The ultimate composite C-brace contributes to the automobile’s 40% torsional stiffness improve whereas lowering mass 55% versus aluminum and 85% versus metal choices. The mixture of upper torsional stiffness and lighter weight excessive on the automobile physique led to a decrease middle of gravity versus conventional supplies.
High down
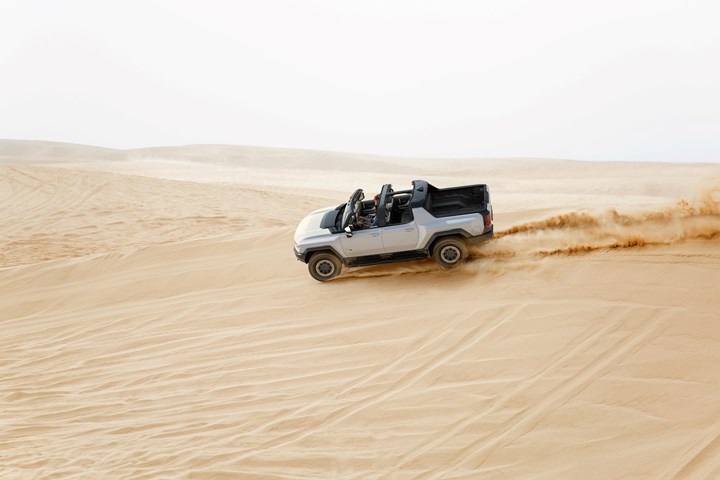
Among the many many equipment that may be ordered for the GMC Hummer EV pickups are both a pair of entrance clear or tinted Infinity glass panels, a single rear Infinity panel or a entrance foldable Sky Convertible High. Picture Credit score: Basic Motors Co.
One other fascinating roof-mounted utility is the body of the Sky Convertible High possibility for 2023 GMC Hummer EV pickups from Basic Motors Co. (Detroit, Mich., U.S.). This light-weight, manually folding smooth high over the entrance seats helps prospects create an open-air expertise with out the necessity to exit the automobile to take away and stow glass Infinity panels that additionally can be found for the automobile, or to fold again and safe different forms of smooth tops.
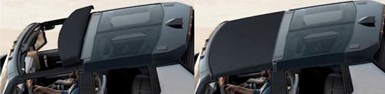
When automobile occupants need sunshine and contemporary air, they will manually fold again the smooth high roof panel and stow it over the middle roof panel (left), then shut it once more (proper) to create a weathertight masking with out leaving the automobile. Picture Credit score: Basic Motors Co.
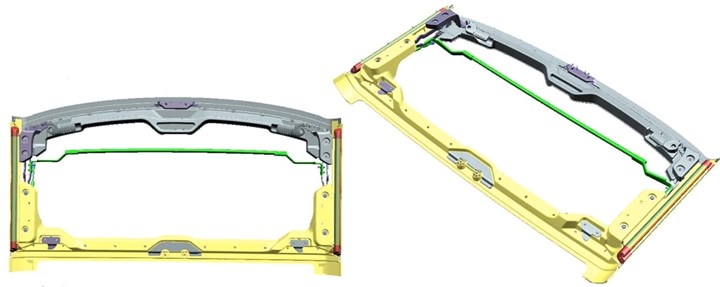
Nearly all of the earlier all-aluminum body for the smooth high panel was transformed to glass/mineral-reinforced PA6 with recycled polymer, lowering mass on the roofline by 1.8 kilograms whereas nonetheless making a weathertight seal. Picture Credit score: Basic Motors Co.
As designed for the Hummer EV, the light-weight unit mixes steel and composite components and gives water sealing and all-weather efficiency — options stated to be unusual with passenger automobile smooth tops — all whereas sustaining occupant security.
GM engineering labored carefully with Tier 1 Bestop Inc. (Louisville, Colo., U.S.) and supplies provider PRET Superior Supplies (Johnsonville, S.C., U.S.) to develop the folding smooth high as an possibility for the pickup. This design changed an all-aluminum body with a hybrid body of aluminum and composite, together with left- and right-side door rails in addition to the rear halo panel — all with molded-in shade (MIC) end — and lowered mass by 1.8 kilograms, which helped enhance automobile dynamics, together with acceleration, braking and cornering.
PRET compounded a 25% quick glass/15% mineral-reinforced PA6 grade (Wellamid MRGF25/15 42H-WBK). In comparison with an all-fiberglass-reinforced grade, the mix of glass/mineral reinforcement is claimed to supply greater warmth resistance, improved mechanicals, lowered warpage and good weatherability. The grade additionally gives glorious floor end, which was in a position to meet GM’s aesthetic necessities with out paint. The compound additionally incorporates post-industrial and post-consumer recycled (PIR, PCR) resin, serving to cut back the manufacturing carbon footprint.
Robust buildings for demanding functions
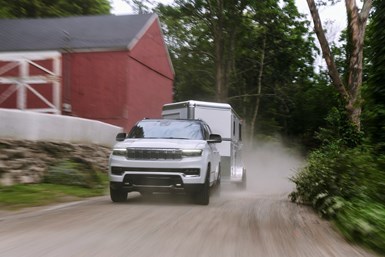
The primary automobile to sport a brand new composite engine stabilizer bracket is the 2022 Jeep Grand Wagoneer SUV. Not solely does the composite bracket facilitate engine insertion on the meeting line but it surely additionally reduces mass by 30% and improves NVH efficiency. Picture Credit score: Stellantis
Three fascinating and totally different makes use of of comparable hybrid composite expertise — which may contain mixtures of steel, steady and/or discontinuous fiber-reinforced composites, and a foaming (increasing) structural epoxy adhesive/sealant — are being utilized in chassis elements on three autos to switch all-metal buildings at much less weight, decrease tooling prices and reductions in NVH. The expertise was developed by Tier 1 L&L Merchandise Inc. (Romeo, Mich., U.S.), which has an extended historical past as an automotive provider of adhesive/sealants, acoustical countermeasures and reinforcement applied sciences that enhance body-in-white (BIW) crash efficiency and occupant consolation and security.
The primary utility is a composite engine stabilizer bracket (CESB) on 2022 Jeep Grand Wagoneer SUVs from Stellantis (Auburn Hills, Mich., U.S.). The bracket, which is positioned between left-hand and right-hand engine mounts, is designed to help with meeting and enhance NVH.
The incumbent bracket was a ribbed construction produced in die-cast aluminum, which required flash removing and secondary machining after casting. Stellantis engineering had already had optimistic experiences changing different mounts and brackets from steel to composite, together with a operating change made on rear differential mounts for the 2020 Jeep Cherokee SUV. In that case, die-cast aluminum was transformed to 50% quick glass/PA6/6 (Ultramid A3WG10CR from BASF), which provided an analogous strength-to-weight ratio however lowered mass by 30%, lowered piece prices and improved NVH due to the 10-times-higher vibration damping of the composite versus steel. In that occasion, the engineering crew reportedly additionally noticed the advantages of BASF’s proprietary Ultrasim anisotropic modeling software program for designing composite elements. They famous that altering from steel to composites for engine and powertrain mounts does necessitate taking a barely totally different design method. Fairly than specializing in simply stiffness based mostly on first-mode targets, analysts want to think about the dynamic efficiency of the system.
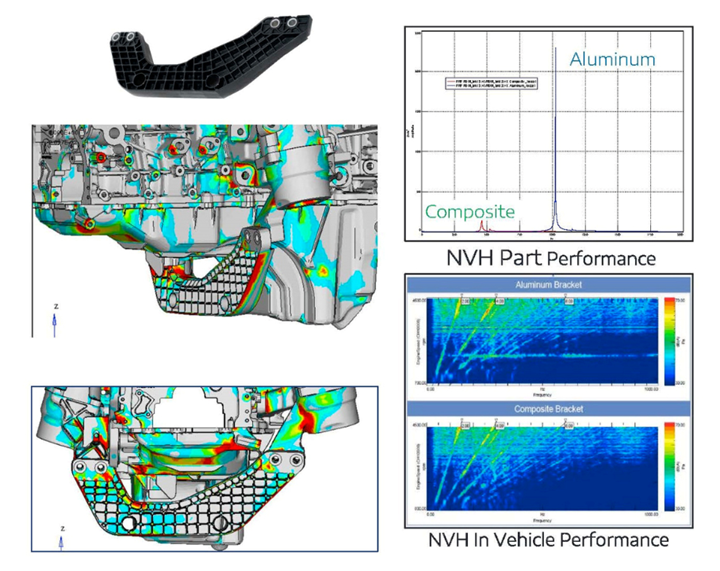
The composite engine stabilizer bracket is designed to assist enhance engine mount stability (lateral rotational stiffness) and cut back transmission of vibrations by way of damping. Picture Credit score: Stellantis
For the brand new CESB undertaking, Stellantis as soon as once more teamed up with BASF in addition to L&L Merchandise to develop the appliance. On this case, a unique polymer system was used. As a substitute of GR/PA6/6, the crew switched to a fiberglass-reinforced thermoplastic polyester mix for a number of causes.
First, on the time the bracket was designed, there was a worldwide scarcity of PA6/6 owing to shortages of adiponitrile (ADN), the important thing uncooked materials used to supply hexamethylene diamine, one in every of two monomers used within the manufacturing of PA6/6. (Throughout the identical interval, uncooked materials prices for aluminum additionally spiked owing to commerce tariffs imposed on imported metals.) Second, switching to a copolymer system involving polybutylene terephthalate (PBT) and polyethylene terephthalate (PET) meant that the ensuing polymer mix has two glass transition temperature (Tg) values as a substitute of only one, which expands the temperature vary the place peak loss issue — a measure of NVH damping — happens. Relying on fiber orientation, chemistry and temperature, thermoplastics comparable to polyamide and polyester usually exhibit 10-20 instances greater loss elements than aluminum. Utilizing the PET/PBT mix improved NVH throughout the complete working temperature vary of the automobile, with peak damping between 55 and 80°C. Third, this explicit composite gives very excessive (>20 gigapascals) modulus due to excessive glass loading plus glorious dimensional stability no matter humidity degree (since PBT and PET are far much less hygroscopic than PA grades).
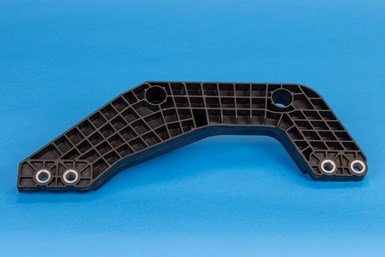
Stellantis reviews the CESB is the primary injection molded bracket that has been used to deck the engine mounts to the physique and likewise reinforce them. It’s additionally stated to be a brand new use for thermoplastic polyesters. Picture Credit score: SPE Automotive Div.
The ultimate design contains a closely ribbed, injection-molded construction of 55% quick glass/PBT-PET (Ultradur B4040 G11 from BASF) plus insert-molded metallic compression limiters. Owing to the larger design freedom provided by injection molding versus die-casting, a brand new rib sample was developed based mostly on CAE simulation of the anisotropic materials. This, together with lowered draft on the software, permitted a tighter rib density whereas lowering materials use versus the die-cast aluminum benchmark. Wallstock was cored out on the attachment factors, eliminating the necessity for post-mold drilling. In truth, the composite half is able to use proper out of the mildew with no secondary machining or different operations required, not like the sooner steel bracket.
The composite bracket additionally gives comparable or higher efficiency than aluminum at 30% decrease mass and seven.5% decrease value, higher NVH and power life that lasts, on common, 4 instances longer (injection mildew versus casting die). Final, however definitely not least, by becoming a member of the 2 engine mounts with the CESB and carrying the meeting into the meeting line by way of the CESB, your entire meeting may be mounted to the automobile body previous to engine set up, making that operation simpler for line employees.
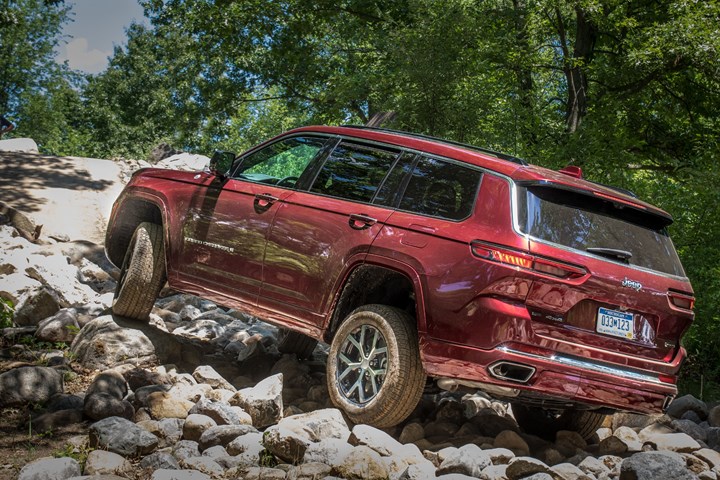
An modern hybrid composite tunnel reinforcement bracket debuted on the usual wheelbase 2021 Jeep Grand Cherokee in addition to the broader wheelbase Jeep Grand Cherokee L SUVs. The bracket is essential for transferring masses from the outer rails to the transmission mounts for improved crash safety as verified by the Insurance coverage Institute for Freeway Security (IIHS) frontal small overlap check and the Nationwide Freeway Visitors Security Administration’s (NHTSA’s) New Automobile Evaluation Program (NCAP) facet affect inflexible pole check. Picture Credit score: Stellantis
One other fascinating composite chassis utility — this time a composite tunnel reinforcement positioned above the exhaust system on 2021 Jeep Grand Cherokee and Grand Cherokee L SUVs — contains a pultruded 80% fiber weight fraction (FWF) steady fiberglass-reinforced polyurethane (PUR) construction (Elastocoat 74850 from BASF) that’s subsequently robotically minimize to measurement after which injection overmolded (together with six aluminum compression limiters and two metal studs) with impact-modified neat (unreinforced) PA6 (Ultramid 8350 HS from BASF).
The supplies are introduced collectively in a rotary injection press with three robots, a number of scanning stations and a laser engraving station. The method creates a light-weight, corrosion-resistant, multi-material 3D half that may carry very excessive axial masses (>70 kilonewtons) but is less complicated to assemble and is more cost effective when it comes to piece worth and tooling funding than the metal benchmark.
L&L Merchandise developed the pultruded insert utilizing a brand new resin system from BASF that — when coupled with steady fiberglass — has a strength-to-weight ratio three to 4 instances greater than both metal or aluminum. Reportedly, the pultrusion course of was enhanced by L&L’s course of/gear enhancements and BASF’s new resin system, which allows two to 3 instances greater throughput than the trade commonplace pultrusion fee of 457-610 millimeters/minute.
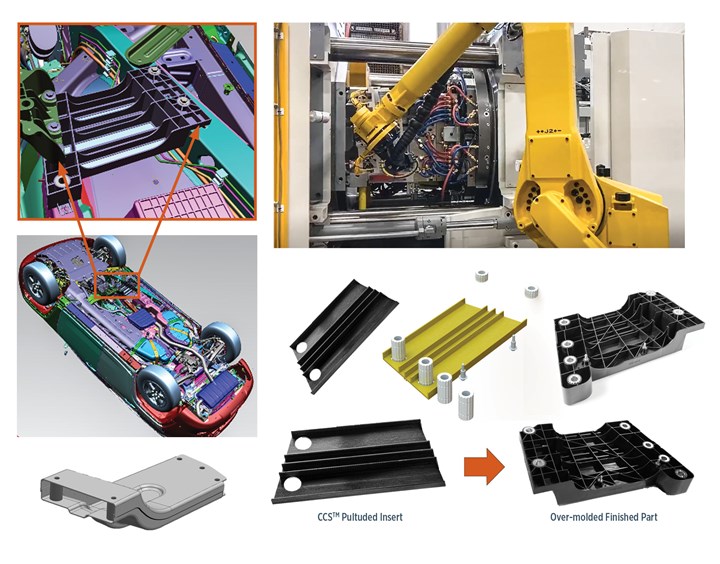
Location of the tunnel reinforcement bracket is proven within the high and center left. High proper reveals a robotic loading the rotary press with elements previous to becoming a member of the pultruded construction and the compression limiters and studs with overmolded impact-modified PA6 (proper center). Alongside the underside, the benchmark-stamped and MIG-welded UHSS benchmark is proven (backside left), together with the pultruded insert (backside center) and the ultimate hybrid composite half (backside proper). Picture Credit score: Stellantis
Quite a few meeting options had been designed in to facilitate meeting for line employees, together with heel-toe for two-way finding; snap options for four-way finding; compression limiters for bolted joint torque retention; and plastic-cutting threaded studs for heat-shield attachment. Moreover, element mass was lowered 40% and subsystem mass by one other 20% (complete weight financial savings was 2.09 kilograms) versus the unique multipiece, stamped and MIG-welded clamshell bracket of ultrahigh-strength metal (UHSS). And it did all of this whereas assembly or exceeding all purposeful necessities. The ensuing hybrid composite construction is claimed to signify a totally new design for a composite tunnel reinforcement and gives an improved load path from rail to transmission assist brackets.
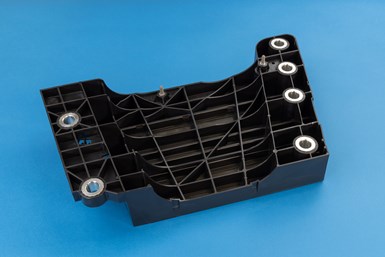
The ultimate hybrid tunnel reinforcement bracket is claimed to exceed the axial load-carrying efficiency of the benchmark UHSS half by 20%. The appliance additionally used a brand new PUR thermoset materials and a brand new methodology for bonding thermoset and thermoplastic supplies with integral {hardware}. Moreover, owing to the design freedom of injection molding, meeting aids had been integrated within the overmolded construction that made automobile meeting simpler for the operator. Picture Credit score: SPE Automotive Div.
Nonetheless one other modern composite chassis utility is a structural cross-member. On typical Ford F-150 pickups, an aluminum cross-car beam — which is mounted within the transverse route beneath passenger seats spanning the gap between driver-side and passenger-side doorways — gives occupant safety within the occasion of a side-impact crash by resisting the tendency of the automobile to buckle across the space of affect. For the all-electric F-150 Lightning mannequin, the place of the battery enclosure and packs encroached into the house the place the aluminum cross-member usually is packaged.
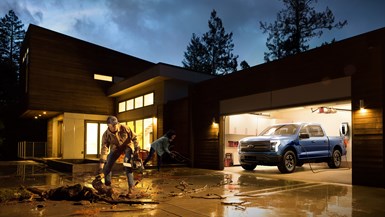
The all-electric Ford F-150 Lightning pickups (above) characteristic a hybrid composite cross-member that protects occupants in addition to the battery pack and is lighter than UHSS metal or aluminum cross-members. Picture Credit score: Ford Motor Co.
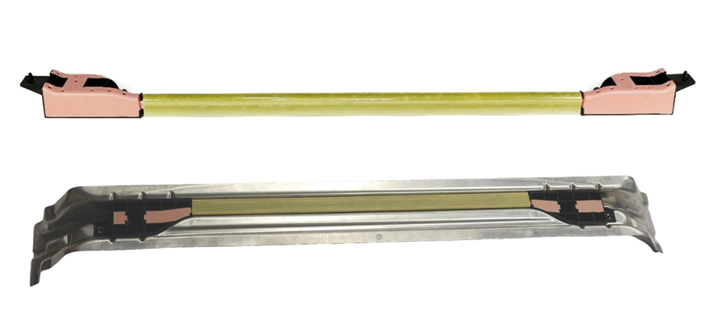
Developed by L&L Merchandise utilizing BASF supplies and its personal foaming adhesive/sealant, the hybrid composite cross-member contains a pultruded steady fiberglass-reinforced PUR beam (gold shade) with endcaps injection overmolded with quick glass/PA6 and structural foaming epoxy adhesive/sealant (pink shade). This hybrid construction is, in flip, slipped into an aluminum stamping (backside, silver) and assembled to the BIW earlier than e-coat. Picture Credit score: BASF Corp.
To guard occupants and the battery packs, Ford engineering teamed with L&L Merchandise and BASF to develop a hybrid composite system. It begins with a hole pultruded beam produced by L&L in 67% FVF/80% FWF steady fiberglass-reinforced Elastocoat 74850 PUR from BASF. The beam is minimize to measurement and L&L’s Composite Physique Resolution (CBS) elements — consisting of a 35% GR/PA6 injection-molded service (Ultramid B3WG7 from BASF) overmolded with L&L’s heat-activated structural adhesive (L-5905) — are inserted into every finish of the pultruded beam to function endcaps. This hybrid meeting is then positioned inside an aluminum stamping, which is subsequently put in on the underside of the BIW. Warmth produced by the e-coat drying/curing course of causes the foaming adhesive/sealant to increase, bonding the composite endcaps to the composite beam, the composite construction to the steel cross-member, and locking your entire construction to the ground of the automobile.
Though this construction is presently solely used on the F-150 Lightning mannequin, the pultruded beam was designed to suit right into a smaller cross-section of the EV’s aluminum cross-car beam in contrast with typical F-150s. Therefore, the composite answer enabled the F-150 Lightning physique construction to hold over the identical mating elements of the aluminum cross-car beam stack-ups from the diesel-model pickup flooring, thus saving Ford from having to make extra capital investments or modifications within the meeting course of. Due to its excessive stiffness/weight ratio, the hybrid construction is lighter and stronger than the unique aluminum cross-member and protects occupants and battery packs throughout extreme crashes at a aggressive worth proposition versus different UHSS or aluminum options.
As these and a rising listing of different functions exhibit, composite supplies — alone or together with different supplies — are offering a slew of advantages not simply to automakers and their half suppliers, however to shoppers and the planet as effectively. With strain to cut back mass rising ever stronger for all classes of passenger autos throughout the trade’s transfer to electrification, anticipate to see composites present up in much more various functions on vehicles and light-weight vans.
Panorama Picture Credit score: Basic Motors Co.